设计开发了基于嵌入式控制技术的FMS刀具控制管理实验系统,其结构紧凑、功能完善、配置灵活,能够模拟FMS实际生产加工中刀具控制过程,既可应用于相关理论与技术的实验验证,也可应用于实验教学和培训。并运用遗传算法在有限刀具资源约束下对FMS刀具调度优化问题进行了研究。采用静态和动态两级调度优化策略,对减少换刀次数,提高FMS生产效率具有积极的作用。
随着零件加工复杂程度和制造精度的不断提高,完整加工技术的逐步应用,数控机床在高精、高速、高效、复合等方面迅速发展,五轴联动控制加工中心也因其更趋向于小批量复杂零件生产而更多地应用于柔性制造系统(FMS)中,这些都标示着柔性制造系统中刀具数量将越来越大,种类将越来越多。如何有效管理品种繁多、规格各异的刀具是当前FMS中的一个关键技术。实际刀具调度控制过程较为复杂,并非所有因素都具有可推理性,仅通过仿真软件所建立的理论模型研究优化的刀具调度控制算法,往往并不能完全反映实际系统的需求,而需要相应的实验条件来模拟运行,以切实可靠的实验数据为基础开展真实有效的研究。
本文首先描述了FMS刀具管理实验系统的总体设计,完成了FMS刀具控制系统软硬件的开发。实验系统硬件部分由容量为160把刀具的中央刀库、刀库进出口站和多自由度换刀机械手等组成。控制系统包括基于嵌入式控制器的刀具控制调度系统和人机界面,实验系统能够根据实际的任务要求来管理、调度刀具。在此基础上,本文根据遗传算法提出了在有限刀具资源约束下对FMS刀具调度优化技术。算法在实验系统上进行了实验验证和比较分析,验证了算法的有效性。
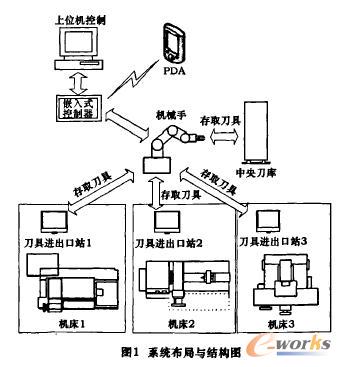
1 FMS刀具控制管理实验系统设计与开发 FMS刀具控制管理实验系统主要由上位机软件控制系统和基于嵌入式控制器的刀具储运系统组成。由多自由度换刀机械手执行换刀操作,系统布局与结构如图1所示。
1.1 FMS刀具控制管理实验系统硬件设计与开发 FMS刀具控制管理实验系统的硬件部分主要是刀具储运系统。笔者设计制作了换刀机械手作为刀具搬运及交换装置,并在已有机床的基础上,设计了中央刀库、刀具进出口站等模拟实际生产加工中的刀具存储系统,从而构成了刀具流的基本硬件结构。换刀机械手及其系统控制器的设计是刀具控制系统硬件部分的核心。换刀机械手主要通过滚珠丝杠、微型齿轮、导轨等机械结构利用电动机驱动实现机械手的多自由度运动。具体机械结构设计不作详细介绍。系统控制器运用嵌人式技术开发,采用PHILIPS公司的ARM7芯片LPC2210作为CPU,有丰富的片内外设,具备JTAG在线调试能力,并在其已有的输人输出口的基础上,通过8255芯片扩展了24路输入输出从而能够满足大量传感器、电动机等输入输出设备接口要求。以太网控制器采用常用的RTL8019AS,以太网接口集成有网络隔离变压器,按照TCP/IP协议进行以太网通讯,能够满足工业要求。控制器通过串口连接无线通讯模块能够实现短距离无线传输;具备USB主机或从机通信功能,从而支持USB接口无线网卡等设备的接人,实现无线网络化控制。该嵌人式控制器具有体积小,功耗低,可靠性高,抗干扰性强,响应速度快等诸多优点,优于PLC等传统控制器。并且,通过移植UC/OS一II嵌入式操作系统,管理机械手自动、手动、各种通讯等多个任务,敏捷性、实时性、灵活性都较高,完全满足实验需求。
1.2 FMS刀具控制管理实验系统控制系统设计与开发
控制系统软件主要是上位机控制软件部分,划分为刀具管理模块,生产计划模块,刀具调度模块,刀具执行模块等,软件框架结构图如图2所示。
(1)刀具管理模块 FMS要实现自动化加工,必须具有刀具管理功能,包括刀具贮存、运输、交换,刀具信息管理,刀具监控等。本文刀具管理主要是刀具信息的管理,采用ADO数据库访问技术管理所有刀具信息。本系统将刀具数据库分为两类,即刀具资源数据库和任务刀具数据库,该模块主要针对这两个数据库进行管理。刀具资源数据库主要存储整个刀具库中所有不同类型刀具的基本信息,通过该数据库可以快速地查询整个刀库中是否存在某刀具,方便了刀具的分配以及刀具基本信息的输人。刀具资源数据库需要根据刀库中刀具的实际变更情况及时更新,从而正确反映当前刀库资源状况。任务刀具数据库在具体任务分配时创建,用于存储实际任务所需的所有刀具信息,该数据库中的刀具是具体任务中刀具调度的对象。由于生产加工过程中刀具状态不断改变,刀具的信息需实时地更新到任务刀具数据库,如刀具的位置,使用寿命,加工精度等,从而保证了任务刀具信息的实时性。该模块是刀具调度的基础。
(2)生产计划模块
生产计划本不属于刀具控制范畴。本系统集成该模块,为实际的任务提供信息输人接口,较方便地实现实际任务信息输人。执行该模块时假设这些信息已经在生产任务调度时分配完毕,通过该模块仅需将机床信息、任务加工工件各工序信息等输人到对应的任务分配数据库。从而为具体的刀具调度提供必要的任务信息。任务所需的所有刀具信息,也需通过该模块逐个写人任务刀具数据库。写人之前,首先需查询刀具资源数据库是否存在该类刀具,若不存在则需要通过某种方式获得,再将其信息导人任务刀具数据库。如果该刀具在任务完成后将作为刀库资源,则还需将该刀具信息添加到刀具资源数据库。通过该模块导人的刀具包括姊妹刀具都有唯一的ID,即实际任务对应的刀具具有唯一的编码,通过ID查询刀具的具体信息方便了刀具调度的实现。
(3)刀具调度模块
实现刀具调度就是按照某种策略、算法,合理安排FMS中的全部刀具活动,目的是将正确的刀具及时准确地装到适当的机床上,最优化地利用系统的生产能力,保证生产加工的顺利进行。刀具调度可分为静态调度和动态调度两种。本系统静态调度主要是加工之前刀具的预分配,由于刀具资源及机床刀库容量的限制,若加工工件所需刀具较多,在加工之前每台机床一般难以分配加工所需的每一把刀具,从而必然会出现机床间刀具互借的情况。如何在有限的刀具资源下给每台机床预分配刀具,使得生产加工过程中机床间刀具交换的次数最少,提高设备利用率及生产效率,是本系统加工之前刀具预分配的目的。在上述各模块的基础上,查询任务分配数据库及任务刀具数据库信息,通过刀具调度模块对这些信息进行分析,运用遗传算法实现在一定刀具资源的约束下预分配所需刀具,并适当调整,直至满足加工要求。生产加工过程中,若某机床加工任务将改变,则需要在当前任务完成之前选择下一个加工任务,查询下一个任务所需刀具的当前信息,并对这些刀具进行调度,当前任务完成之后,按照结果将下一任务所需刀具搬运到该机床,从而使得刀具调度时间和任务加工时间充分重叠,提高了调度效率。动态调度能够在线实时处理生产加工过程中的刀具活动,实现实时的刀具过程控制。如加工过程中机床缺少某种刀具或者多台机床同时争用同一刀具,则调度模块响应需求,首先搜寻该刀具是否有姊妹刀具,然后按照一定的调度策略对所需刀具进行调度,将所需刀具分配到对应的机床上,从而保证加工的连续性,最大限度地提高设备的利用率。
(4)人机控制界面模块 该模块主要用于实现换刀机械手及刀库的上位机控制,包含上位机操作界面,可以通过计算机控制刀具的储运、换刀等现场作业过程,能够设置多种通讯方式进行通讯,如以太网、RS232,无线,USB等,满足工业现场的多种需求。通过该界面可以选择控制模式:面板控制模式,可以通过操作面板控制换刀机械手,一般用于现场控制;上位机控制模式,该模式下只能通过计算机对换刀机械手进行控制,能够实现远程的操控;网络控制模式,可以利用PDA等移动设备通过无线网络进行控制,PDA控制界面如图3所示。各模式单次仅一种有效,系统默认设置为面板控制模式,可以直接进行面板操作。该模块实现了换刀机械手的上位机控制,是工业现场控制的有效补充,是远程监控得以实现的重要组成部分。
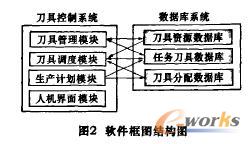
分页
2基于遗传算法的刀具优化调度技术研究
本文提出的FMS刀具调度优化技术采用两级优化控制技术:即刀具静态调度优化和动态调度优化。
静态调度优化策略:在有限刀具资源的约束下给每台机床预分配加工所需刀具,使得生产加工过程中机床间刀具借用的次数最少,从而充分提高机床及刀具的利用率。其基本步骤是:首先,初始化算法参数和任务参数,充分利用有限的刀具资源在机床刀具库容量的约束下产生第一代种群,计算该种群中各个体对应的适应度值,统计第一代种群数据,将该种群中的最佳个体信息存人最佳信息结构体。按设定的概率选择较优的个体作为父体,采用轮盘赌选择法进行选择,以设定的交叉率及变异率进行交叉和变异操作,并调整为满足约束要求的子个体,重复该操作直至产生设定个数的子个体。计算各子个体对应的适应度函数值,并与父体一起按照适应度函数值排序,从中选择数量为种群大小之多的较优个体作为下一代种群个体,从而生成新一代种群,并将最佳个体信息记录在最佳信息结构体中。在设置的最大世代数内不断进化、计算、统计,最终搜寻一个最优的个体使得适应度函数的值为最大值。可以多次调整遗传算法参数进行计算,从而选择多次执行结果中的最优解作为最佳结果,最后按照编码原则对最优解进行解析,按照解析结果进行解析,适当进行刀具分组分配,并输出显示。
动态调度优化策略:刀具动态调度优化遵循以下3个原则。①停滞时间最优原则:当加工零件某工序缺少某把刀具时,优先选择可最快获得的刀具;②刀具寿命分配最优原则:当多把刀具符合加工要求时,优先选择刀具寿命类型为青壮型的刀具。(根据刀具使用时间将刀具分为三种类型:低于刀具寿命30%为青壮型,处于刀具寿命30%~65%之间为中和型,高于刀具寿命65%为老衰型);③刀具与零件精度要求匹配最优原则:根据零件的加工精度需求,优先选择符合精度要求的匹配指数最高的刀具。根据以上原则并由实际情况分配各自权重进行计算,使在线调度达到最优化。
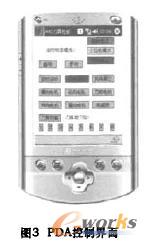
3实验验证与实验结果比较
实验参数如下:机床5台,加工工件数6件(各不相同),每台机床的刀具库容量设为30,生产加工刀具总数108,其中设定有多个刀具为短缺资源(以工件1为代表,列出其工序及对应的加工刀具信息如表1所示)。拟定遗传算法参数如下:种群大小50,最大遗传代数500,变异率0. 005,交叉率0. 4。将机床信息、刀具信息、各工件加工信息等输人对应数据库,运用遗传算法进行计算以寻找最优刀具分配。此外,笔者特地采用启发式算法进行了计算。通过本文开发的刀具管理实验系统,能够实验模拟实际的生产加工,对两种理论算法结果进行验证,结果比较如表2所示。
由表2可以看出,运用遗传算法优化调度分配,加工过程中机床间刀具的交换次数较启发式算法要少,机床利用率较高,是较有效的刀具调度优化方式。通过不断模拟实际的生产加工,实验系统硬件及软件不断改进至完善,最终该实验系统模拟结果能够与实际结果有较好的吻合。该实验平台对于相关理论的验证有着非常重要的作用,并且由于实验平台很好的模拟性和嵌人式技术开发的先进性,已应用于实验教学并收到良好的效果。
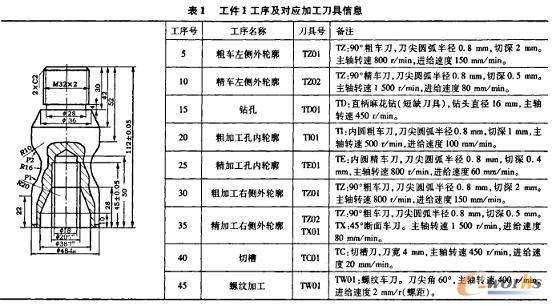

4结语 本文针对FMS刀具管理控制优化技术研究的需求,设计开发了FMS刀具管理控制实验系统,该系统基于嵌人控制技术开发,具有结构紧凑、功能完善、配置灵活等特点,能够模拟FMS实际生产加工中刀具控制过程,既可应用于相关理论与技术的实验验证,也可应用于实验教学和培训。
运用遗传算法在有限刀具资源约束下对FMS刀具调度优化问题进行了研究,采用静态和动态两级调度优化策略,实验证明和其他算法相比较对减少换刀次数,提高FMS生产效率具有积极的作用。