汽车轮毂的拓扑优化设计
发布时间:2017-10-12
作者:
张帅 张琦 贾祥磊
来源:新浪博客
为了实现汽车铝合金轮毂的结构轻量化设计,本文以拓扑优化方法为理论依据,结合有限元分析技术,针对特定的铝合金轮毂结构进行了轻量化研究。
0 引言
在能源、环境和安全三大问题的迫切要求下,现代汽车节能降耗要求不断高涨,安全和环保法规日趋严格,汽车轻量化是必然趋势。轮毂是汽车的一个重要部件,关系着汽车行驶的安全和舒适性,铝合金轮毂具有诸多优越性已经得到广泛应用,短时期内很难找到替换材料,因此合理的轮毂结构就变得尤为重要,良好的轮毂结构具有重量轻,性能好,材料利用率高,便于加工等优点。传统的优化是在设计经验的基础上反复试验,计算和校核,其优化周期长,并且耗费大量的人力和物力,近几年出现了采用结构拓扑优化思想和有限元模拟相结合的优化方法,能够更科学和高效的实现结构的轻量化设计。本文以苏州三基铸造装备股份有限公司生产的轮毂为例,以轮辐和轮毂中心区域为设计变量,采用有限元模拟的方法对轮毂进行拓扑优化设计,并依据最终的拓扑优化结果建立了新轮毂几何及有限元分析模型,对此模型进行了静态力学分析,验证了优化结果的准确性。
1 拓扑优化技术简介
拓扑优化技术能在给定的设计空间内找出最佳的材料分布,拓扑的改进可大大改善结构的性能和减小结构的质量。目前连续体结构拓扑优化技术比较成熟的是均匀化方法、变密度方法和变厚度方法。
变密度法就是引入一种假想的密度值在[0,1]之间的密度可变的材料,将连续结构体离散为有限元模型后,以每个单元的密度为设计变量,将结构的拓扑优化问题转化为单元材料的最优分布问题。用变密度法得到的拓扑优化结果是密度等值分布图,其中密度为中间值所对应的区域为假想的人工材料,在实际的工程中是没法实现的,因此在得到最优拓扑图形后要对这些区域进行人为的处理以适应实际的工程需要。
2 轮毂拓扑优化有限元仿真
本文采用HyperWorks的OptiStruct模块进行轮毂的拓扑优化设计,建立了轮毂的有限元模型。有限元模拟中网格的剖分质量是影响计算精度的重要因素,因此本文用专业的有限元前处理软件HyperMesh来生成高质量的网格,然后进行边界条件和相关参数的设置并进行求解。轮毂的结构优化设计由轮辐部位的优化和在轮辐优化基础上的轮毂中心部位的优化组成。
2.1 有限元模型及主要参数
对轮毂三维模型(图2-1)进行处理后在HyperMesh中划分高质量的网格,共1160370个单元,288,104个节点,其中轮辐部位为24817个penta6单元,其余为tetra4单元。依据轮毂的实际工况建立了轮毂的有限元模型,其主要参数设置如下:
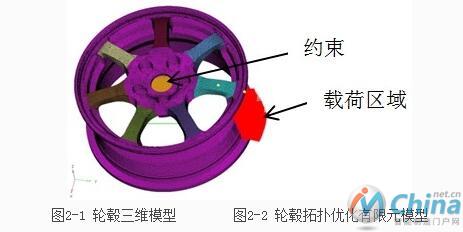
-
约束:在轮毂轴承装配处建立刚性单元,完全约束其6个自由度,从而将轮毂固定住。
-
载荷:0.65MPa。小汽车重约2吨,车轮触地面积65*120mm2。
-
载荷施加部位:一种是对应轮辐的轮辋区;另一种是加在两个轮辐中间部位的轮辋区。(优化结果相似,此处取一种)
2.2 轮辐部位拓扑优化有限元仿真
2.2.1 轮辐部位拓扑优化主要参数设置
-
制造约束:最大最小尺寸、拔模方向、模型重复等求解约束
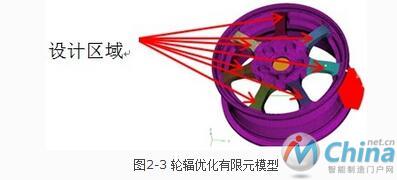
2.2.2 轮辐部位拓扑优化结果及模型重构
图2-4是密度值取0.3时的轮辐部位优化结果,可以看出优化后的轮辐结构近似为在中间区域开了一个槽。故对原模型重构如图2-5所示。
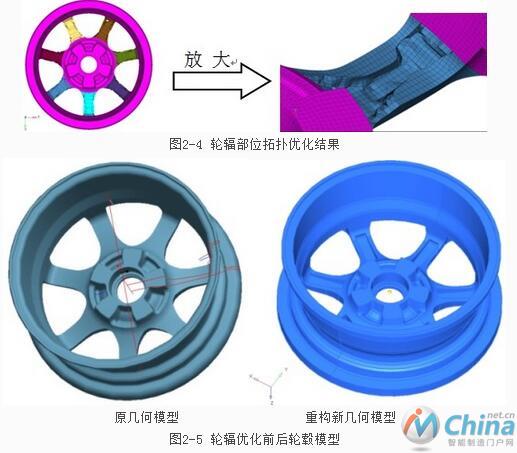
2.2.3 重构模型性能验证
对轮毂轮辐部位优化前后的模型进行静态的应力分析,对比两者的应力云图可得(表2-1),优化前后的分布应力相当,优化后最大应力略有增大为62.6Mpa,但是低于A356铝合金常温下许用极限为112.5MPa,满足性能要求。
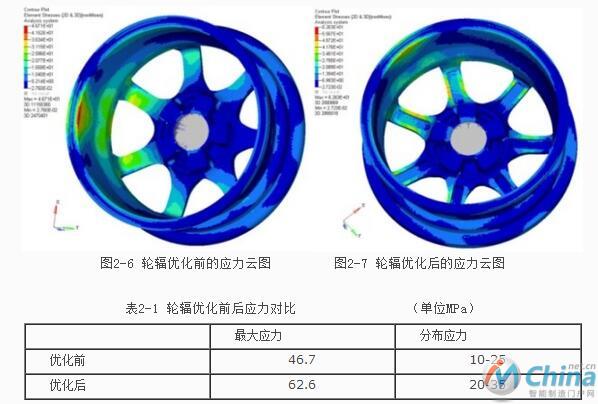
对轮毂轮辐部位优化前后的模型进行静态的位移分析,对比两者的位移云图可得(表2-2),优化后位移虽略有增大为0.56mm,但是小于1mm,且两者分布位移相当,满足要求。
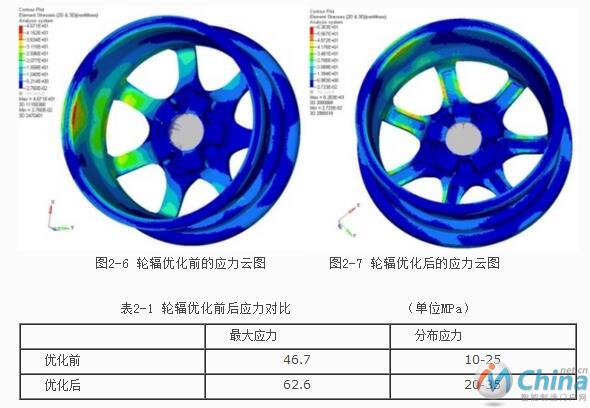
2.3 轮毂中心部位的优化
在轮辐优化的基础上进一步对轮毂中心部位进行优化,为了获得更好的优化效果,对原轮毂部位进行改动,使优化的变量范围扩大,如图2-10所示。
图2-10 优化区域的还原
2.3.1 轮毂中心部位拓扑优化主要参数设置
本文来源于互联网,e-works本着传播知识、有益学习和研究的目的进行的转载,为网友免费提供,并以尽力标明作者与出处,如有著作权人或出版方提出异议,本站将立即删除。如果您对文章转载有任何疑问请告之我们,以便我们及时纠正。联系方式:editor@e-works.net.cn tel:027-87592219/20/21。